Printing keyboard, also known as a keypad printing, features silicone rubber buttons with colorful symbols or icons printed on their surfaces. There are two main printing methods used for these keyboards: silk screen printing and transfer printing. When the silicone rubber buttons’ surface is uneven, transfer printing is often chosen to achieve a better and more consistent print quality. This method ensures that the printed symbols remain clear and durable, enhancing both the functionality and appearance of the keyboard.
Details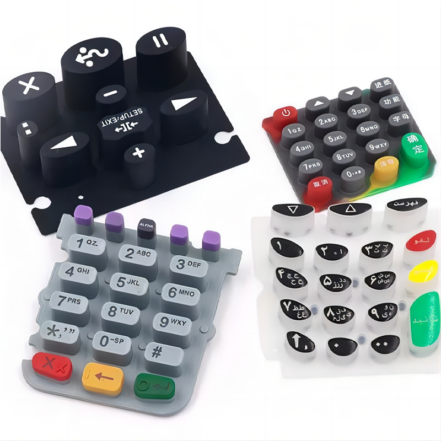
– Origin:Xiamen, China
-Brand:OEM
– Keypad Material:Silicone
– Key Features:Durability, Chemical Resistance, Weather Resistance, Temperature Tolerance
– Applications:Home Appliances, Industrial Equipment
– Custom Orders:Accepted
– Color Options:Multicolor Printing
– Materials:Silicone, PVC, PET, PC, Metal, Adhesive-Backed Materials
– Environmental Considerations:Eco-friendly inks and materials
– Size:Customizable
– Logo:Custom Branding Available
– Accepted Artwork Formats:AI, PDF, CDR
Surface Treatments for Keypad:
- Silk Screen Printing: This method applies a durable ink layer to the surface, ideal for creating high-contrast legends and intricate designs.
- Laser Etching: Utilizes a laser to engrave designs onto the keypad, offering precision and permanence for long-lasting markings.
- Epoxy Coating: Provides a clear, protective layer over the keypad’s surface, enhancing durability and resistance to wear and tear.
- PU Coating: A polyurethane coating that offers protection against scratches and abrasion while maintaining a smooth finish.
- UV Coating: Cures under ultraviolet light to create a robust, protective layer that resists fading and enhances durability.
- Matte Finish: Applies a non-glossy surface treatment to reduce glare and provide a soft, textured feel.
- Glossy Finish: Creates a high-shine, reflective surface that enhances the visual appeal and makes the keypad easy to clean.
- Textured Coating: Adds a tactile texture to the keypad, improving grip and usability, especially in high-touch areas.
- Color Coating: Involves applying various colored coatings to achieve vibrant hues and custom color matching.
The Production Process of Conductive Keypad:
Design: Create a detailed design considering form, key layout, and structure.
Material Preparation: Gather conductive materials like silicone rubber, carbon powder, metals, and backing material.
Conductive Layer Formation: Develop the conductive layer using silicone rubber mixed with carbon powder or metal mesh.
Printing: Use advanced printing methods to apply key patterns and symbols onto the conductive layer accurately.
Assembly: Integrate the conductive layer with the backing material, ensuring precise alignment.
Curing: Subject the keypad to controlled curing to enhance adhesion.
Quality Testing: Thoroughly test sensitivity, electrical conductivity, and aesthetics.
Packaging: Securely package the keypads to protect against damage during transportation.
Reviews
There are no reviews yet.