What Is LSR Injection Molding
Liquid Silicone Rubber (LSR) Molding is an advanced manufacturing process designed to produce durable, flexible, high-precision, and high-quality parts in large quantities. This technique is particularly effective for creating silicone rubber keypads and other components that require precise dimensions and exceptional performance.
Liquid Silicone Injection Molding yields parts that exhibit excellent water repellency and resistance. Due to these properties, along with their precise sizing, LSR-molded components are ideal for applications such as seals, membranes, electrical connectors, and a wide range of medical, commercial, and domestic uses.
The liquid injection molding process involves injecting liquid silicone rubber into pre-made molds. Once injected, the material cures within the mold, and the process is repeated to complete the production run. This method ensures consistent quality and reliability, making it suitable for silicone rubber keypads and other products designed to withstand demanding conditions across various industries.
Liquid Silicone Rubber Molding Capabilities
At Siliconekeytech, we provide comprehensive preliminary design guidelines that outline our extensive molding capabilities. These guidelines are designed to assist you in developing custom designs with enhanced features, aesthetics, and reduced production timelines. Below are the details of our capabilities:
Capabilities | US | Metric |
Size | 12 in. x 8 in. 4 in. | 304.88mm x 203.2mm x 101.6mm |
Volume | 13.3 cu. in. | 217,948 cu. mm |
Depth | Maximum 2 in. from parting lines. | Maximum 50.88 mm from parting lines. |
Projected Mold Area | 48 sq. in. | 30968 sq. mm |
Machining Tolerance | +- 0.003 in. | +- 0.08 mm |
Linear Tolerance | +- 0.025 in./in. | +- 0.025 mm/mm |
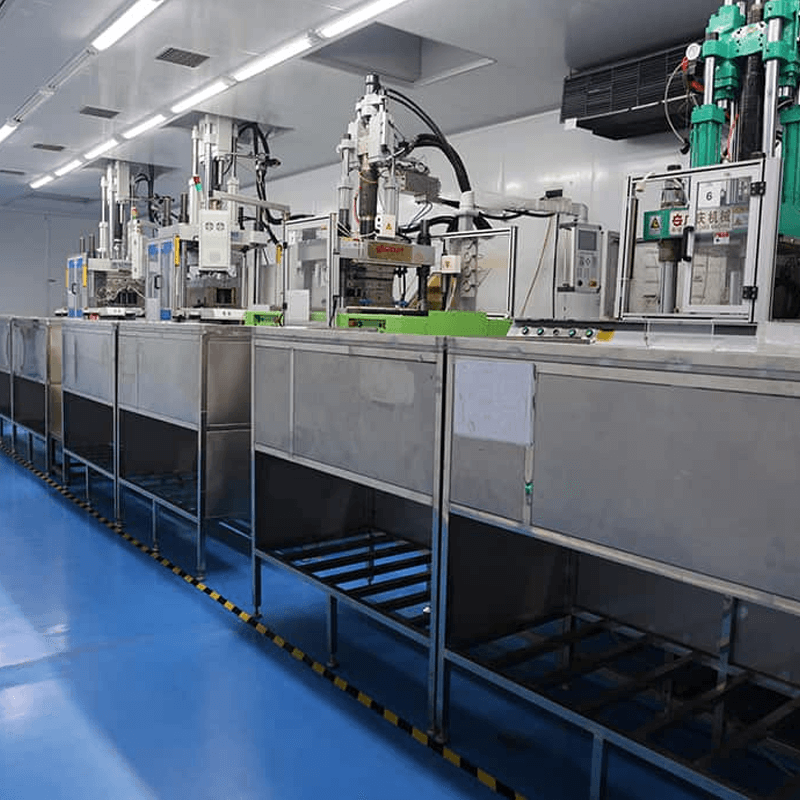
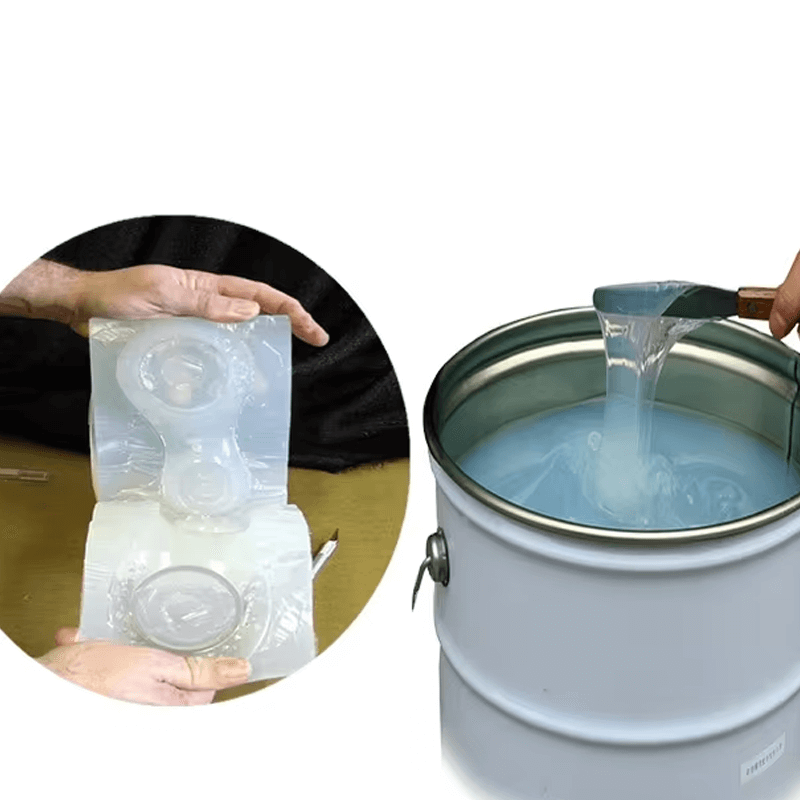

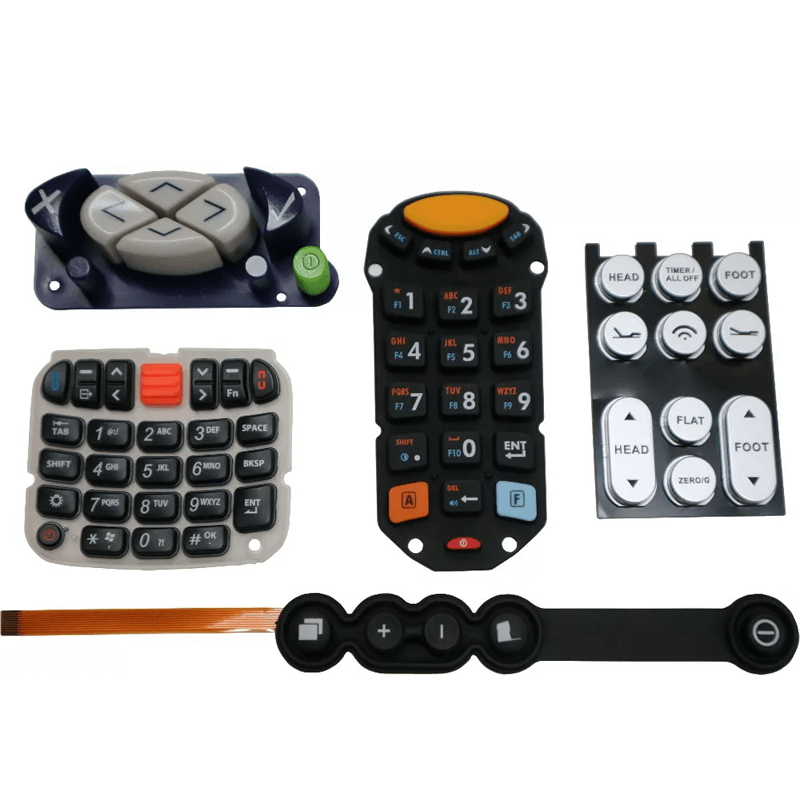
Why Choose Us for LSR Injection Molding
With over two decades of experience, Siliconekeytech has manufactured billions of custom parts for our partners. We continuously advance our technology and expertise to deliver precise, reliable, high-quality LSR components. Our commitment to innovation provides significant advantages, including:
- Advanced Molds and Automation: Our Class 101 LSR production molds and automated handling systems are designed for continuous, hands-free production. These systems are integrated with our cutting-edge molding technology to ensure optimized manufacturing, enhanced productivity, and high-yield output.
- Innovative Molding Technology and Quality Assurance: We utilize state-of-the-art LSR molding technologies, including LSR 2-shot, LSR overmolding, and LSR multi-shot processes. Certified to ISO 9001, ISO 13485, and IATF 16949 standards, our quality metrology lab, proactive quality planning, and dedicated project management ensure consistently high-quality parts.
- Value-Added Operations: Our integrated approach includes planning and automating post-molding operations within the manufacturing cells. Secondary processes are performed robotically to enhance precision, streamline manufacturing processes, and shorten supply chains, adding significant value.
- Versatile Part Geometries: We leverage the strengths of LSR and liquid injection molding to produce a broad range of part geometries, from simple to complex and small to large, using single or multiple materials. Our extensive expertise in LSR technologies positions Siliconekeytech as a leader in producing high-quality silicone rubber keypads and other custom components.
Choose Siliconekeytech for your LSR injection molding needs to benefit from our advanced technology, precision, and comprehensive services.
Characteristics Of Liquid Silicone Rubber (LSR)
Biocompatibility: Liquid Silicone Rubber (LSR) exhibits exceptional biocompatibility, having undergone extensive testing to ensure it is compatible with human tissue and body fluids. Unlike other elastomers, LSR resists bacterial growth, does not stain or corrode, and is both tasteless and odorless. It can be formulated to meet stringent FDA standards and is sterilizable using various methods, including steam autoclaving, ethylene oxide (ETO), gamma irradiation, and e-beam techniques.
Durability: LSR components are highly durable and can endure extreme temperatures, making them ideal for applications in automotive engines and other high-heat environments. Unlike plastic injection molded parts, LSR parts are fire retardant and do not melt, ensuring greater reliability and safety.
Chemical Resistance: LSR demonstrates strong resistance to water, oxidation, and a range of chemical solutions, including acids and alkalis. This chemical stability makes it suitable for demanding applications where chemical exposure is a concern.
Temperature Resistance: Molded silicone, such as Silastic LSR by Dow Corning, offers impressive temperature stability, maintaining its properties from -60°C to +180°C. This wide temperature range ensures reliable performance across various conditions.
Mechanical Properties: Liquid Silicone Rubber provides excellent mechanical performance with high elongation, tear and tensile strength, and flexibility. It features a hardness range of 5 to 80 Shore A, making it versatile for different applications, including silicone keypads.
Electrical Properties: With outstanding insulating capabilities, LSR is an excellent choice for electrical applications. It performs reliably in extreme temperatures, offering superior insulation compared to conventional materials.
These attributes make LSR an optimal material for silicone keypads and other precision-engineered components requiring high performance and durability.
Advantages of LSR Injection Molding
1. Design Flexibility: Liquid Silicone Rubber (LSR) injection molding facilitates the creation of intricate part geometries and technical solutions that are not achievable with other molding methods. This flexibility is ideal for producing complex silicone keypads and other advanced components.
2. Consistency: LSR injection molding ensures the highest level of consistency in product dimensions, precision, and overall quality. This high degree of accuracy is essential for producing reliable silicone keypads and other precision-engineered parts.
3. Precision: The process is characterized by flashless and wasteless tool design concepts, accommodating parts ranging from 0.002 grams to several hundred grams. This precision is crucial for manufacturing detailed silicone keypads with exacting standards.
4. Reliability: Utilizing the latest technology in machinery, tooling, and automation, LSR injection molding offers exceptional reliability, ensuring consistent performance and quality throughout production.
5. Quality: The process achieves a zero-defect quality level through rigorous in-process controls, guaranteeing that each silicone keypad and other components meet stringent quality standards.
6. Speed: With short cycle times, LSR injection molding supports high-volume production, from several thousand to millions of units, making it an efficient choice for large-scale manufacturing.
7. Cleanliness: Production is conducted in state-of-the-art Class 7 and 8 cleanrooms, ensuring that the process is clean and contaminant-free, which is particularly important for sensitive applications.
8. Cost-Effectiveness: LSR injection molding offers a low Total Cost of Ownership, providing an economically advantageous solution for producing high-quality silicone keypads and other components.
Overall, LSR injection molding delivers a consistent, efficient, and cost-effective method suitable for a diverse range of applications, including the precise manufacturing of silicone keypads and other advanced components.