What Is Multi-color Dripping Molding
Our multi-color dripping molding service combines solid silicone rubber and liquid silicone rubber into a single product stream, offering customizable color options without affecting the silicone's quality. This process involves mixing the two silicone materials in specific proportions, followed by vacuum processing, which enhances color performance while maintaining cost-efficiency and production volume.
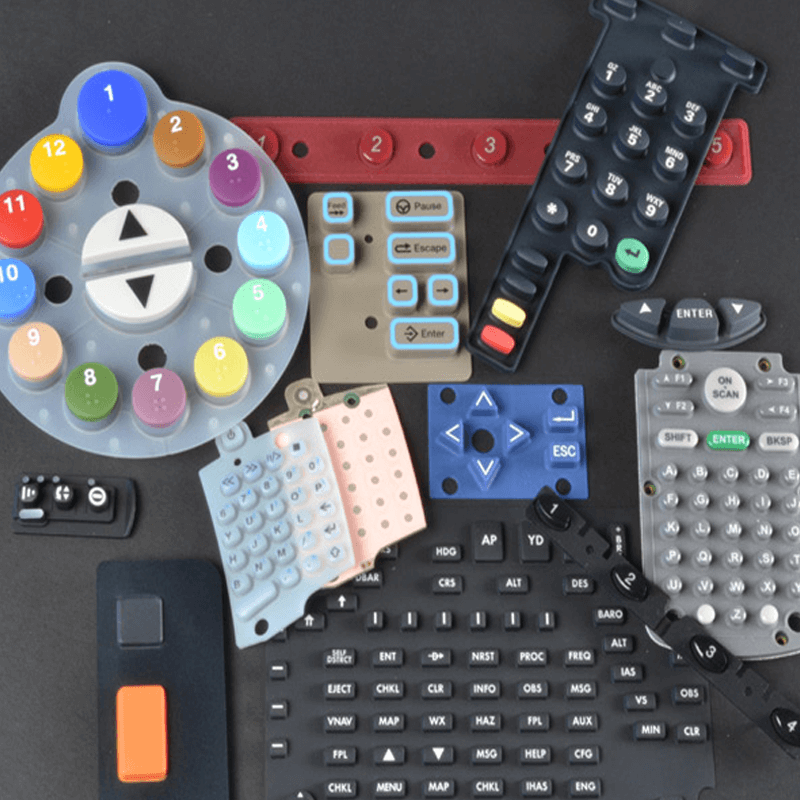
Characteristics of Multi-Color Dripping Molding
Multi-color dripping molding (epoxy molding) utilizes a combination of solid silicone rubber and liquid silicone rubber to produce a single, cohesive product stream. This technique allows for adjustable colors in the liquid silicone without compromising the quality of the final product, making it ideal for complex, multi-colored silicone products.
Key characteristics include:
- Versatile Color and Pattern Options: Capable of integrating 2-12 colors and various patterns, this method offers extensive customization for design flexibility.
- Wide Application Range: Suitable for a variety of applications, including silicone keypads, licensed character products, gaming peripherals, movie and animation merchandise, and promotional gifts.
- Enhanced Visual Appeal: Perfect for creating vibrant, eye-catching products with intricate color designs, suitable for industries that require detailed and aesthetically pleasing components.
Multi-color dripping molding is particularly effective for producing silicone rubber keypads and other silicone-based items where both functionality and visual appeal are essential.
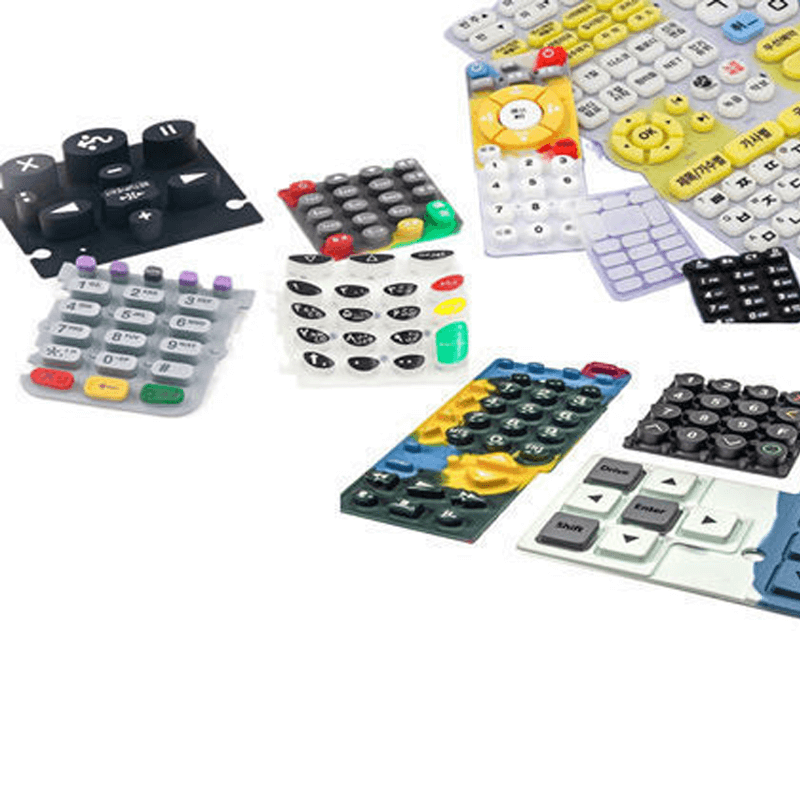
Design and Materials for Multi-Color Dripping Molding Products
When designing multi-color silicone products, including silicone keypads, the co-injection dripping molding process is utilized to achieve vibrant, multi-colored results. To ensure manufacturability and high-quality output, several factors must be considered from the design phase:
- Material Selection: Choose between liquid silicone rubber (LSR) or high-consistency rubber (HCR), based on the required properties and end-use of the product.
- Durometer and Hardness: Select appropriate hardness (Shore A) to match the functional needs of the silicone keypads and other components.
- Color and Design: Define color choices and patterns to ensure compatibility with the molding process and to prevent issues like color bleed or peeling.
- Dimensional Accuracy: Ensure precise dimensions and tolerances to achieve reliable, large-volume production with minimal scrap rates.
Our experienced engineers provide expert guidance in material selection and design to optimize the manufacturability of multi-color silicone products, including custom silicone keypads. This approach minimizes waste and maximizes production efficiency while delivering high-quality, visually appealing results.
Multi-Color Dripping Molding Process
The multi-color dripping molding process involves several key steps to produce high-quality silicone products, including silicone rubber keypads:
1. Material Application: Liquid silicone material is applied to the tooling using a dripping machine, allowing for precise control over the color and pattern of the silicone keypads.
2. Heating and Solidification: The tooling is then heated to cure the liquid silicone, solidifying it into the desired form. This step ensures that the silicone rubber achieves the necessary durability and stability.
3. Insertion and Vulcanization: Solid silicone rubber is placed into the tooling, where it undergoes vulcanization. This process solidifies the rubber further, creating a robust and functional part.
4. Tooling Efficiency: While this molding process may be slower than traditional injection molding, it offers quick turnaround times for prototype and R&D parts. Additionally, it requires lower upfront tooling costs. For cost-effective production, creating high-multiple cavity tooling can enhance efficiency.
This process is particularly effective for producing detailed, multi-color silicone keypads and other intricate silicone products, offering both flexibility and cost savings in manufacturing.
Advantages of Multi-Color Dripping Molding Process
1. Enhanced Design Flexibility: Multi-color dripping molding allows for the creation of intricate, multi-colored patterns on silicone keys. This versatility is ideal for producing visually appealing and complex designs.
2. Cost-Effective Prototyping: The process is particularly advantageous for prototyping and R&D. It offers quick turnaround times and lower tooling costs compared to traditional molding methods, making it ideal for developing new silicone key designs.
3. Precision Color Application: Dripping molding enables precise control over color application, ensuring consistent and high-quality color placement on silicone keys. This results in vibrant, uniform finishes.
4. Reduced Tooling Costs: Multi-color dripping molding involves lower initial tooling costs compared to some other molding processes. This makes it a cost-effective option for manufacturing silicone keys, especially in the early stages of product development.
5. Lower Scrap Rates: The process minimizes material waste by allowing for precise application and curing of silicone. This efficiency helps reduce scrap rates and production costs.
6. High-Quality Aesthetics: The technique produces silicone keys with high aesthetic quality, thanks to the ability to create detailed multi-color patterns and textures. This is beneficial for applications requiring both functionality and visual appeal.
This approach is particularly well-suited for creating custom silicone keys with intricate designs and vibrant colors, offering both practical and aesthetic advantages.
Quality Standards for Multi-Color Dripping Molding Silicone Products
Material Standards: All silicone products, including silicone keypads, adhere to stringent material standards, such as FDA and LFGB certifications, ensuring safety and quality for various applications.
Size and Tolerances: Precision is key, with size tolerances maintained within ±0.15 mm, or as specified in the 2D drawings. This ensures accurate and consistent dimensions for silicone keypads and other products.
Surface and Color Quality: Rigorous quality checks are performed to ensure the absence of surface defects such as damage, lack of adhesive, deformation, color inconsistencies, and material overflow. This guarantees a high-quality finish for every silicone product, including silicone keypads.
Silicone Keypad Specific Standards: For silicone keypads, additional quality standards include ensuring tactile responsiveness, durability under repeated use, and proper alignment with electronic components. These standards are critical to ensuring optimal performance and user satisfaction.