What Is LSR Insert Molding
Insert molding is a sophisticated manufacturing technique that integrates metal or other components into a plastic part during the molding process. This method significantly enhances the structural integrity, functionality, and performance of the final product.
The process starts with creating a mold, which acts as the negative form of the intended plastic part. Before injecting the plastic, a metal insert—ranging from threaded fasteners to complex metal components—is strategically positioned within the mold.
Molten plastic is then injected into the mold, enveloping and bonding with the metal insert as it cools and solidifies. This results in a composite structure that leverages the strengths of both materials, providing a silicone keypad with enhanced durability, strength, and precision.
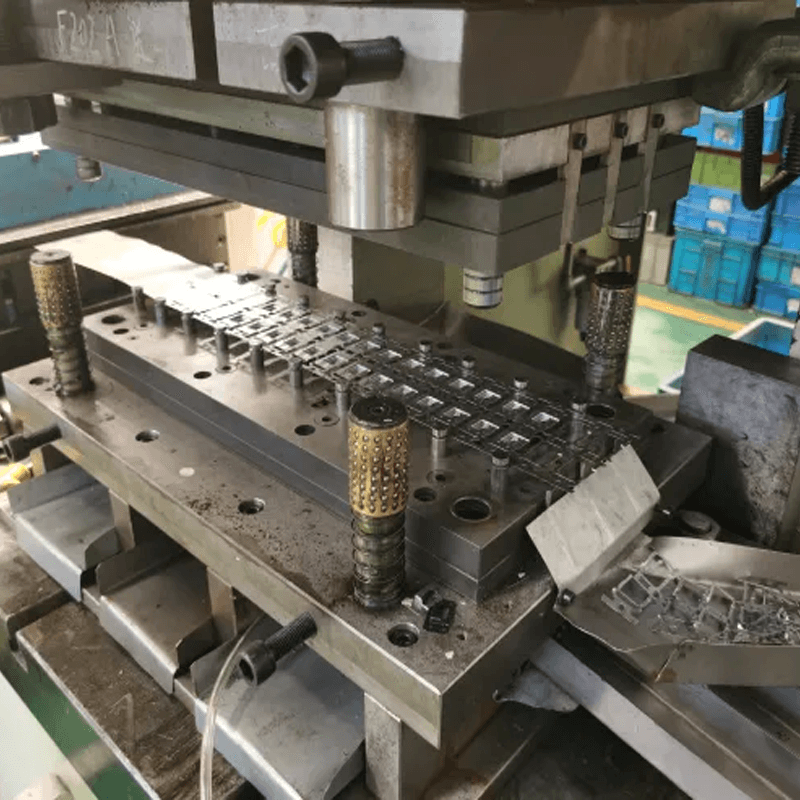
Advantages of LSR Insert Molding for Silicone Keypads
1. Enhanced Strength and Durability: LSR insert molding integrates metal inserts with silicone rubber in silicone keypads, significantly improving their mechanical strength and durability.
2. Complex Geometries: This process allows for intricate designs in silicone keypads by embedding metal inserts, providing greater design flexibility.
3. Cost Efficiency: Combining silicone rubber and metal inserts in a single production step reduces overall manufacturing costs for silicone keypads compared to traditional methods.
4. Streamlined Production: LSR insert molding consolidates the molding of silicone rubber and the insertion of metal components into one efficient process, simplifying production.
5. Improved Thermal Conductivity: Metal inserts in silicone keypads enhance thermal conductivity, making them suitable for applications with specific thermal requirements.
6. Weight Reduction: Despite adding metal, LSR insert molding can reduce the weight of silicone keypads by strategically placing reinforcements.
7. Customization of Properties: Various metal inserts can be used to tailor the electrical conductivity, magnetic properties, or other functional characteristics of silicone keypads.
8. Reduced Assembly Time: Integrating metal inserts during the molding process eliminates the need for additional assembly steps, reducing overall assembly time for silicone keypads.
Why Choose Us for Molded Inserts?
Extensive Choices: Access a vast array of material combinations, finishes, tolerances, markings, and certified options tailored to your specific needs. Whether you're seeking advanced solutions for silicone rubber keypads or other custom parts, we offer unparalleled flexibility and variety.
User-Friendly Experience: Simplify your procurement process with our seamless service. Receive your silicone rubber keypads and other parts directly at your doorstep, avoiding the complexities of sourcing, project management, logistics, and shipping arrangements.
Verified Network: Our stringent certification process includes ISO 9001:2015 and IATF 16949:2016, ensuring that only top-tier suppliers meeting the highest standards are part of our network. This guarantees that your silicone rubber keypads are produced by exceptional shops adhering to rigorous quality standards.
Expertise in Custom Solutions: Benefit from our extensive experience and expertise in mold design and development. We offer comprehensive support from prototyping to full-scale production, ensuring that your silicone rubber keypads meet precise specifications and performance requirements.
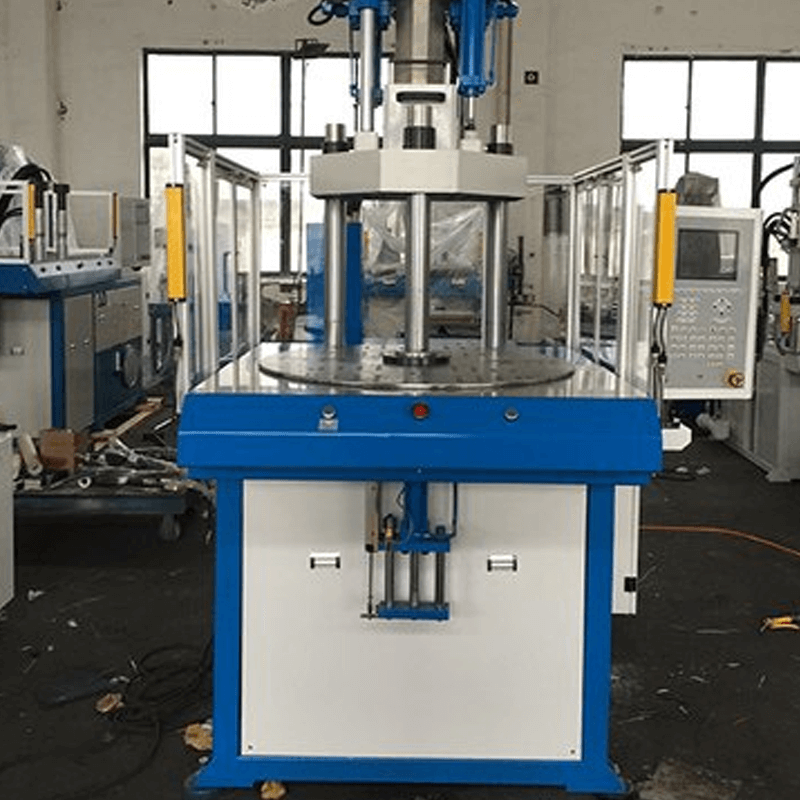
Comparison: LSR Insert Molding, Overmolding, and Injection Molding
LSR Insert Molding and Overmolding are advanced manufacturing techniques used to integrate distinct components into a single, cohesive part. Here’s a detailed comparison of these processes with a focus on applications like silicone keypads:
LSR Insert Molding: This technique integrates preformed inserts, such as metal components, into a plastic part within a single molding cycle. For example, in the production of silicone keypads, a metal insert can be embedded in the silicone rubber during the molding process. The technique starts with placing the insert into the mold, followed by the injection of molten silicone rubber. As the material cools and solidifies, it encapsulates the insert, creating a durable, unified component. This method is ideal for applications requiring enhanced strength and functionality.
Overmolding: Overmolding involves a two-step process where an initial part is molded first, and then a second layer of material is applied. For instance, in the production of silicone keypads, an initial rigid plastic base can be molded, followed by an overmolding process to apply a softer silicone layer. This creates a single part with varied material properties, enhancing tactile feedback and grip. Overmolding is used to add functional or aesthetic layers to existing components, resulting in improved ergonomics and performance.
Injection Molding: Traditional injection molding involves forming a single part by injecting molten plastic resin into a mold. This process can also be used to encapsulate smaller components, such as threaded rods or bushings, within the resin. In the context of silicone keypads, injection molding can include encapsulating silicone rubber around functional inserts or structural components to create a complete part.
In summary, LSR insert molding is a single-step process that integrates inserts into silicone keypads, while overmolding applies an additional layer of silicone to an existing plastic base in a two-step process. Both techniques are subsets of injection molding, offering unique advantages for creating complex, high-performance components.
LSR Insert Molding Applications
LSR insert molding is widely utilized across various industries, offering solutions for a range of applications including:
- Automotive Components: Enhancing the durability and performance of automotive parts with integrated metal inserts.
- Industrial Equipment: Providing robust and reliable components for heavy-duty machinery and industrial systems.
- Medical Devices: Ensuring precision and functionality in critical medical devices through advanced molding techniques.
- Consumer Products: Creating high-quality, durable products that meet consumer demands for performance and aesthetics.
- Electrical Parts: Integrating metal inserts to improve the functionality and reliability of electrical components.
With extensive experience and expertise in LSR insert molding, we are equipped to handle the complexity of your projects. Request a quote today or contact us for comprehensive injection molding services tailored to your specific needs.